- News and Events
- News
- 2023.09, BRING ON THE NEW NORMS
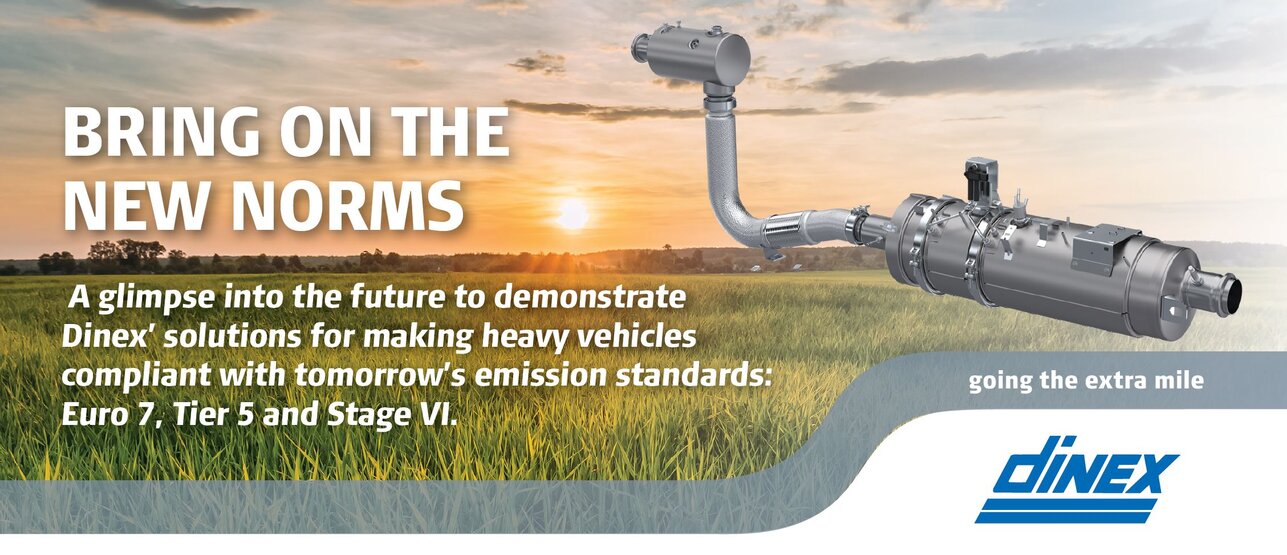
Diesel exhaust aftertreatment concept for heavy duty EU 7 engines

System Integration: More tech, Same space
By Arun Guruvaraju
Mobility keeps getting cleaner. That is a clear fact when lookingat the proposed future Euro 7, Tier 5 and the expected upcoming Stage VI emission standards.
Significantly more stringent limits to especially the levels of NOX emissions, regulation of even smaller particles (PN), and the inclusion of N2O in the scope, are expected to be a reality for European Heavy-Duty trucks in less than 5 years. At Dinex, thetechnology to solve these challenges is already known and far along in development.
Temperature is already a key element of all AfterTreatment Systems (ATS), and future solutions will increasingly rely on technologies such as advanced insulation, insulated decoupling, electric heatersand optimized, compact layouts.
The biggest change will be the introduction of dual-stage SCR concepts. For the general system layout, this means, that the key technologies will no longer be fitted only in a single box. There will be a Prebox and a Mainbox - in this article, we will explain the difference.
Prebox
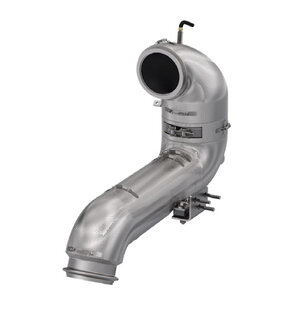
The purpose of the prebox is to gain as much utilization of the exhaust heat as possible. This will enable an early start of injection of the AdBlue® for the NOX reduction, and therefore it must be fitted very close to the engine. It has been a challenge that calls for clever system design down to each component. Space is tight near the engine, so the prebox needs to be compact and still contain the necessary components; electric heater, urea dosing & mixing, flexible element, and in some cases also the first in a series of SCR-substrates (depending on application).
To avoid the risk of Urea deposit formation, the mixer needs to be extremely compact and still highly efficient. In addition, the insulation needs to be effective and compact to protect nearby components from thermal impact of the e-heater and exhaust gas.
All in all, integrating a prebox in an already complex system is a complex engineering challenge. Despite this, Dinex has proven it to be doable by using own technologies and innovative solutions, which are scalable to individual customers requirements.
Mainbox
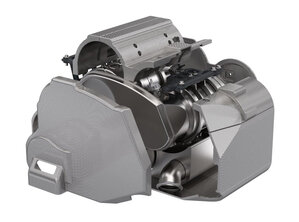
At first the Mainbox may seem similar to a Euro 7 aftertreatment system as the wellknown the key catalyst functions are present; Diesel Oxidation Catalyst (DOC), Diesel Particulate Filter (DPF) and SCR catalyst including injection and mixing of Urea. But from there, the resemblance stops. If not included in the Prebox, the Mainbox also contain the first of two SCR catalysts in front of the DOC.
The tighter performance requirements make it necessary to set new standards for temperature retention, mixing efficiency and NOX conversion rate. All without compromising acoustic performance and simultaneously respecting increased durability requirements, and still designed in the same limited space available.
This does not leave much room to design an optimized solution, but with Dinex’ patented compact mixing technologies and versatile layout concepts, chances are that the right application specific solution is just around the corner.
Dinex is ready for future emission standards with in-house developed technologies and innovations. Through a series of 4 articles, 4 technical experts from around the Dinex Group each highlights the many challenges of the tightened regulations they work with in their everyday and presents the technical solutions which are already available.
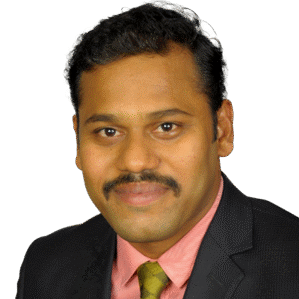
Arun Guruvaraju
- Bsc. Mech.Eng.
Project Manager with specilty in System Integration of complex Emission AfterTreatment Solutions
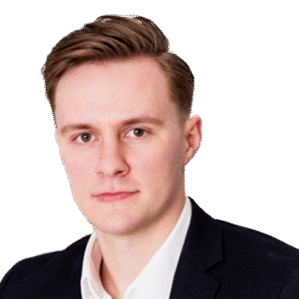
Konstantin Bondarev
- Bsc.Eng & PMP
R&D Project Manager with specialization in thermal management (e.g. passive insulation and active heating).
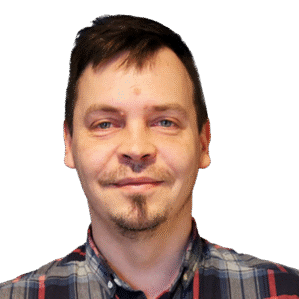
Toni Korhonen
- Bsc. Mech.Eng.
Senior Design Specialist with years of experience in transforming innovations to applications
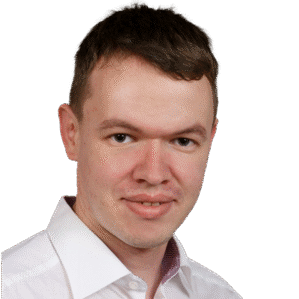
Dr. Mirko Pfeifer
Specializes in development of catalytic coatings to match future regulations and customer demands
A glimpse of the Dinex OEM Division
Global Footprint - Local Presence
Operating with local teams close to our customers, backed up by global technical competences.
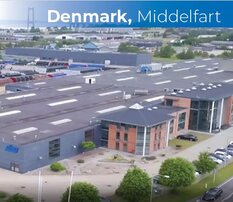
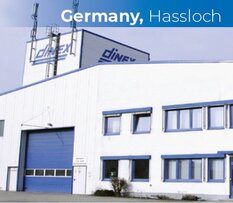
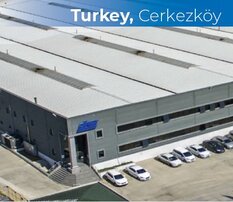
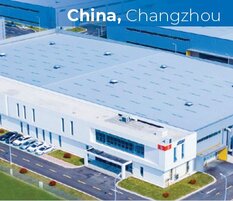
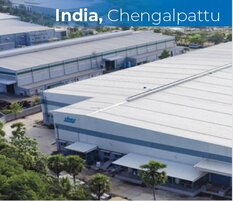
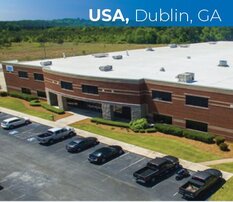
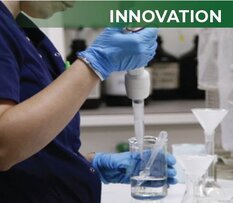
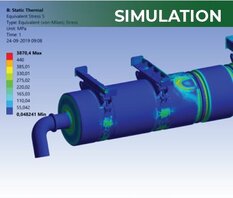
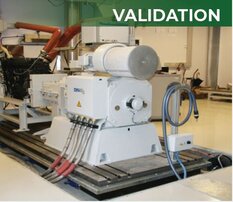
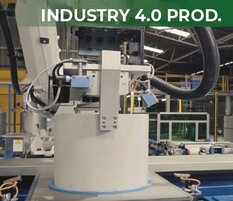
Core Technologies - Proven Solutions
All developed and produced in-house for a simple, cost efficient supply chain with highest solution ownership.
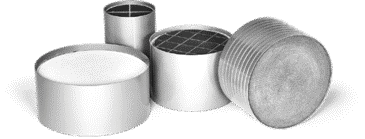
Ceramic and Metallic
Substrates with catalytic coating
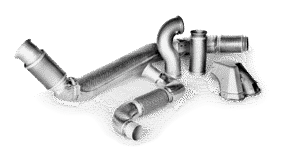
Pipes, Zero-Leakage Decoupling
and Thermal Management
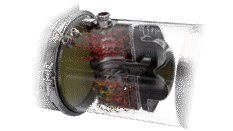
Canning and system integration
with optimal flow and mixing
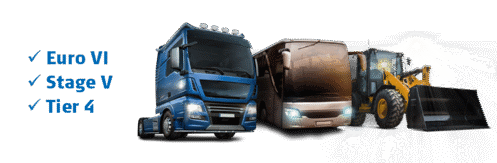
Agile Partnership - Customized Innovations
Full System and customer specific engineering approach: From final application down to coating formula.
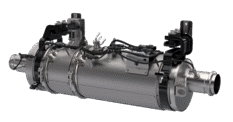
In-line system
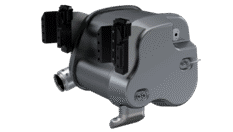
Box system
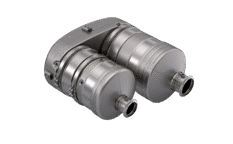
U-Shape system
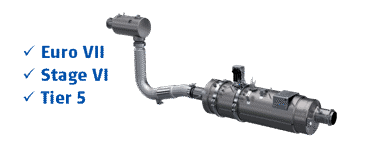
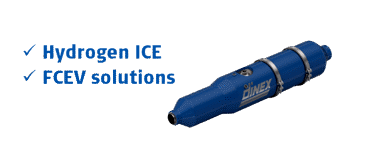